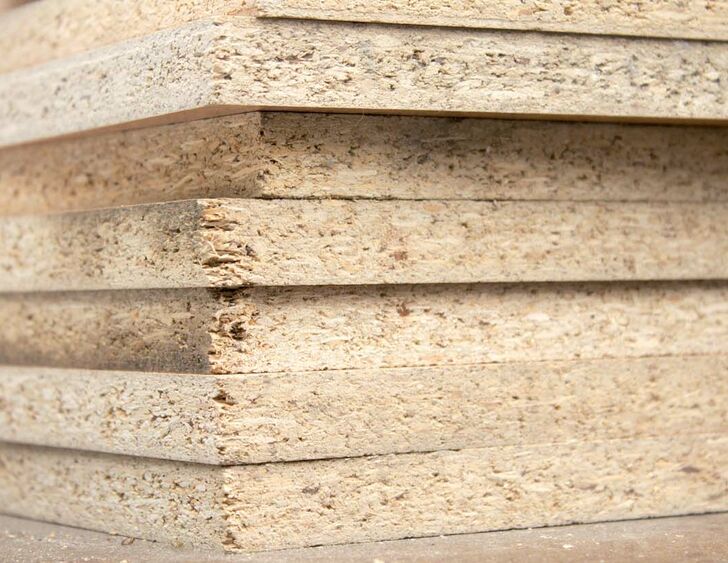
En construction, tout comme en aménagement intérieur, le bois massif s'est fait supplanter par des panneaux de bois à la composition et à l'utilisation très variés. De l'OSB au contreplaqué, le bois se réinvente pour répondre à des exigences très diverses.
Les grands principes des panneaux de bois
Pour fabriquer des panneaux, il faut du bois, de l’eau, de la chaleur, de la pression et quelques adjuvants. La distinction entre les différents produits obtenus tient au process de fabrication et à la nature de la matière première.
S'ils sont regroupés sous la même dénomination, les panneaux de bois se suivent mais ne se ressemblent pas, qu'il s'agisse de leur aspect extérieur ou encore de leur utilisation. En effet, entre le panneau de particule, le panneau de fibres, le panneau OSB ou encore le contreplaqué, les applications sont aussi diverses que variées tous comme les contraintes techniques. Aussi pour faire le bon choix et sélectionner le matériau le plus adapté aux travaux que vous souhaitez entreprendre (gros-oeuvre, construction d'étagères ou réalisation de cloisons, ...) mieux vaut savoir s'y retrouver dans la diversité de panneaux de bois que l'on trouve dans le commerce.
S'ils sont regroupés sous la même dénomination, les panneaux de bois se suivent mais ne se ressemblent pas, qu'il s'agisse de leur aspect extérieur ou encore de leur utilisation.
Le panneau de particules
Le matériau principal reste le bois, plus exactement les sous-produits issus de la fabrication des éléments en bois massif. L’industrie du panneau recycle ainsi tout ce qui n’est pas exploitable, depuis les coupes d’éclaircie jusqu’au recyclage de produits transformés, en passant par les bois ronds (petits bois, branches, grumes déclassées) ou les rebuts de scierie (copeaux, plaquettes, sciure, etc.).
L'agglo ou aggloméré
La définition exacte de l’agglo ou aggloméré est un panneau dit de process (PP), constitué de particules de bois (grands copeaux, particules, copeaux de rabotage…) et/ou autre matériau lignocellulosique (chanvre, lin bagasse), non orientées (en vrac), avec addition d’un liant, organique ou minéral. Le panneau se compose en général de plusieurs couches de particules avec des parements plus résistants et fins que la partie centrale. Il existe des panneaux pour milieu sec ou humide, dans les classes de risque 1 et 2.
Les panneaux de particules sont définis par la norme NF EN 309 et leurs exigences sont spécifiées par la norme NF EN 312, qui détermine sept types de panneaux :
– Type P1 - Exigences pour panneaux pour usage général en milieu sec.
– Type P2 - Exigences pour panneaux pour agencements intérieurs (dont les meubles) utilisés en milieu sec.
– Type P3 - Exigences pour panneaux non travaillants en milieu humide.
– Type P4 - Exigences pour panneaux travaillants utilisés en milieu sec.
– Type P5 - Exigences pour panneaux travaillants utilisés en milieu humide.
– Type P6 - Exigences pour panneaux travaillants sous contrainte élevée utilisés en milieu sec.
– Type P7 - Exigences pour panneaux travaillants sous contrainte élevée utilisés en milieu humide.
En France
il y a deux labels de qualité : le panneau de particules CTB-S pour usage en milieu sec en construction, répondant au type P4, et le panneau de particules CTB-H pour milieu humide répondant au type P5. Ces derniers sont en général de couleur verte. La qualité E1 ou ½ E1 sont des gammes de panneaux dont les émanations de formaldéhyde sont réduites.
L’épaisseur courante des panneaux débute vers 10/12 mm jusqu’à 30/35 mm. Les plus minces sont utilisés en plafond suspendu, parement de cloison légère, structure d’ameublement. Les épaisseurs moyennes sont conçues pour résister à des charges d’exploitation, pour les dalles de plancher ou la tabletterie. Enfin, les plus épaisses sont généralement réservées à des applications particulières, comme les plans de travail, par exemple.
Les panneaux de particules sont disponibles sous différentes formes, standard, bruts à deux faces poncées, ou revêtus sur deux, quatre ou six faces. Les panneaux mélaminés sont recouverts d’une feuille de papier imprégnée de résine, pressée à chaud. Les panneaux finish foil sont revêtus d’une feuille de papier décor collée sur le support.
Le panneau de fibres
En pulvérisant la matière première, il n’en reste plus que les fibres, très fines. Le classement des différents panneaux de fibres dépend de leur densité et du mode de fabrication, par voie sèche ou humide.
Sèche ou humide
Les panneaux de fibre, type MDF, sont fabriqués par un procédé à sec. Les fibres sont liées entre elles (82 %) par une colle synthétique (10 %, eau et adjuvants 8 %). Les panneaux obtenus sont classés selon leur masse volumique (densité), HDF, MDF, LDF ou ULDF. Les premiers ont été fabriqués en 1966 aux USA, en 1973 en Europe. Fabriqués en plusieurs couches, la partie centrale est moins dense que les parements.
Les panneaux MDF sont disponibles dans des épaisseurs allant de 1,8 à 60 mm. Les largeurs courantes varient de 1 220 à 1 850 mm, pour des longueurs pouvant atteindre 3 660 mm.
Les produits en bois comprimé sont sensibles à l’humidité. Toutefois la qualité CTB-H permet un usage en milieu humide classe 2.
Les panneaux de fibres durs, anciennement dénommés isorel, sont fabriqués par voie humide à partir d’une sorte de pâte à papier pressée très fortement à chaud. Ce procédé évite le recours à des liants. Ils présentent une seule face lisse. Ils sont très résistants à l’humidité et servent aussi bien à l’agencement intérieur, en panneau de sous-toiture ou à l’emballage (cageots de fruits et légumes).
Les panneaux de faible densité de type ULDF perdent leur performances mécaniques, et acquièrent des capacités isolantes. Il s’agit des panneaux isolants en fibre de bois dont la masse volumique est inférieure à 350 kg/m3 et dont le coefficient de conduction thermique est compris entre 0,037 et 0,070 W/m2 K. Cette qualité les classe parmi les meilleurs isolants thermiques, d’hiver et d’été. C’est un isolant non toxique, non irritant, facile à manipuler, affichant d’excellentes performances acoustiques.
L’OSB est utilisé pour des applications structurelles en construction, notamment pour les planchers, les toitures et les parois de mur.
Le panneau OSB
Après les fibres et les particules, lorsque la taille des copeaux augmente, les modes de fabrication s’adaptent. Et les performances mécaniques aussi.
Oriented Strand Board : OSB
Le nom est l’acronyme anglais de Oriented Strand Board. En français, ce nom devient panneau de lamelles minces, longues et orientées. Si cela donne une bonne indication sur le procédé de fabrication, l’acronyme OSB reste plus facile à retenir. Il s’agit donc d’un panneau composé de lamelles disposées en couches, pressées et collées ensemble. Dans les couches externes, les lamelles sont généralement orientées parallèlement à la longueur du panneau alors que dans la couche médiane les lamelles sont perpendiculaires. Les lamelles sont fabriquées comme des copeaux de taille-crayon. Leur taille moyenne est de 10 cm de long pour 5 mm à 5 cm de large et 0,5 à 1,5 mm d’épaisseur. Le collage est généralement une combinaison de Phénol-Formaldéhyde (PF), Mélamine-Urée-Formol (MUF) et isocyanates (PMDI). Ces liants apportent aussi la résistance à l’humidité. La masse volumique de l’OSB varie de 600 à 680 kg/m3. Les dimensions standard sont celles des autres panneaux, 2 440 x 1 200 mm, 2 440 x 1 220 mm et 2 500 x 1 250 mm, dans des épaisseurs allant de 6 à 40 mm. L’OSB est utilisé pour des applications structurelles en construction, notamment pour les planchers, les toitures et les parois de mur.
Il existe quatre classes d’OSB définies dans la norme EN 300 en termes de performances mécaniques et de résistance à l’humidité (classes d’emploi 1 et 2).
- OSB/1 - Panneaux pour usage général et panneaux pour agencements intérieurs (y compris les meubles) utilisés en milieu sec
– OSB/2 - Panneaux travaillants utilisés en milieu sec.
– OSB/3 - Panneaux travaillants utilisés en milieu humide.
– OSB/4 - Panneaux travaillants sous contrainte élevée utilisés en milieu humide.
Le contreplaqué
Les Finlandais sont les premiers producteurs européens de contreplaqué et le Royaume-Uni le premier consommateur, les deux volumes étant pratiquement à égalité (1,2 millions de m3 ).
Feuilles de bois
Le contreplaqué est fabriqué à partir de feuilles de bois déroulé, calandrées, séchées, orientées, encollées et pressées. Les différentes superpositions peuvent être homogènes mais, le plus souvent, la qualité des feuilles, voire leur épaisseur, varie suivant leur disposition.
Léger et facile à installer, le contreplaqué offre une excellente résistance à la déformation. Ses couches croisées lui confèrent une bonne stabilité et une grande résistance aux chocs. Les caractéristiques mécaniques des panneaux de contreplaqué varient en fonction de leurs compositions (espèces utilisées, nombre et épaisseur des plis). Il n’y a pas de valeurs normalisées universelles pour les propriétés mécaniques du contreplaqué. Elles sont adaptées en fonction de la composition de chaque produit.
Le contreplaqué se classe en fonction du type d’emploi :
Classe 1 : intérieur sec
Classe 2 : intérieur humide
Classe 3 : extérieur
Un panneau classé E1 dégage moins de 0,1 ppm de formaldéhyde selon la norme EN 717-1.
Les dimensions courantes varient de 6 à 30 mm en épaisseur, pour des largeurs de 1 250 ou 1 500 mm et des longueurs de 2 500 ou 3 100 mm pour des panneaux entiers.
Le contreplaqué est proposé dans une large gamme d’aspects : brut, poncé deux faces, replaqué, etc. Toutes les essences de bois peuvent être mises en œuvre pour des applications intérieures (classe d’emploi 1 et 2). À l’extérieur, en revanche, pour une classe 3, il faut utiliser une essence résistante, naturelle ou conférée.
Les faces apparentes du contreplaqué sont généralement en okoumé, pin maritime, peuplier, ou épicéa. Pour des applications spécifiques, telles que les coffrages ou les planchers d’échafaudage, le contreplaqué peut être filmé (bakélisé). Enfin, il existe deux certifications de qualité, NF extérieur CTB-X et NF Coffrage CTB-C.
Réputation et histoire
Des colles dangereuses ?
Les colles employées dans la fabrication des panneaux de fibres ont la réputation d’être mauvaises pour la santé. En particulier le formaldéhyde utilisé comme liant dans le MDF est réputé cancérigène. Malheureusement ce composant continue à s’évaporer après fabrication. Depuis les années 2010, les autorités européennes, suivant en cela les autorités californiennes, pionnières en la matière, abaissent le plafond d’émission de composés de formaldéhyde. Pour les panneaux de particules les seuils réglementaires US (auxquels nous sommes calés en France depuis mars 2019,) sont inférieurs à 0,05 ppm (0,05ml/m3 ) pour le contreplaqué et inférieurs à 0,09 ppm pour le panneau à particules...
Aggloméré, MDF, une histoire industrielle
Dérivé d’un procédé inventé dans les années 1920 par un certain William H. Mason, ingénieur américain, le MDF est le fruit d’une erreur technique. Le MDF est véritablement né dans les années 1960, sa commercialisation prend de l’ampleur dès les années 1970 aux États-Unis. À cette époque, les coupes de bois « à blanc » (tous les arbres d’une parcelle sont coupés, il ne reste plus rien) fournissent à l’industrie des panneaux dérivés des arbres fins, petits et donc non valorisables en menuiserie traditionnelle. Ce type de coupe étant de moins en moins pratiqué, les fabricants de médium utilisent désormais des cartons de recyclage, des chutes de papier : le bois lui-même entre de moins en moins dans la composition des panneaux MDF. Écologie oblige ! L’aggloméré de bois vendu sous forme de panneau est une réponse industrielle à deux besoins. D’une part la nécessité d’utiliser au mieux (c’est-à-dire d’accroître la valeur du bois de coupe) le matériel ligneux et d’autre part de répondre aux besoin de l’économie en crise de l’entre-deux-guerres.
Le panneau d’aggloméré, inventé en Allemagne dans les années 1930, a véritablement pris son essor dans les années 1950. Le produit est alors en parfaite adéquation avec l’urgence de la reconstruction. Le panneau (d’aggloméré ou MDF) est en effet un produit standard, fiable dans le sens où contrairement au bois brut il n’est pas sujet aux variations dimensionnelles, qui s’intègre parfaitement dans les procédés mécanisés de la construction actuelle. Toutefois, les fabricants de panneaux sont confrontés au renchérissement inexorable de la matière première. Les déchets de scierie, bien que renouvelables, sont devenus un matériau rare parce que de plus en plus réservés aux pellets et autres granulés, mieux valorisés. C’est ainsi que de matériau «pas cher», le panneau d’aggloméré devient un matériau «un peu cher».